製造系KAIZEN研究所を開設しました
フェースブックを使ったオンラインサロン(非公開グループ)を開設しました。
名前は「製造系KAIZEN研究所」です。
基本的には製造業における改善の進め方や考え方、各種手法の使い方などの実践的な部分、状況によってはメンバーからの質問などにも答えたいと思っています。
最初の100名くらいまではほぼ無条件で入会審査OK!となると思いますので、入会の方、よろしくお願いします(無料です)。
たぶんフェースブック上で検索すれば見つかると思います(入会申請してください)。
そもそも何でオンラインサロンを始めたのかと言いますと、やっぱり日本の没落と言いますか、30年近くにわたって経済成長が止まったままで、気が付いたら中国や東南アジア諸国とほとんど差が無い所まで来てしまった日本を強く憂いてという事になります。
いわゆる国際的地位の地盤沈下とも言えますが、私はこうなってしまった原因の大きな部分を日本の製造業の低迷が占めているのではないかと思っています。製造業に深く携わっているものとして、過去の日本の輝きを知っているものとして「本当にこのままで良いの?」というのが製造系KAIZEN研究所を作ろうと思った発端です。
トップ画面に「日本のモノづくりを再び世界一に」と記しているのは、まさにそのイメージを表現しているつもりです。
具体的な中身はこれから作っていく事になると思いますが、日本の製造業の発展に寄与することは何でも話題にしていきたいなと思っています。特に会社を大きく変えるためのイノベーションをどう仕掛けるか、と言ったような話題にも乗りますし、今作業改善のこんなところで困っている!と言った相談事にも積極的に対応して行くつもりです。
日本の成長のためには日本の「製造業」を変える!
↓
日本の製造業を変えるためには「各企業」が変わる!
↓
各企業を変えるためには内部の「人」が変わる!
↓
人が変わるためには「知識・技術・経験」を身に着ける!
そして知識・技術・経験をこの製造系KAIZEN研究所で学んでいただければと考えています(経験については他の人の経験の追体験になるとおもいますけどね)。
まだまだどう進んで行くのかは分かりませんが、取り敢えずよろしくお願いします。
台湾産パイナップル
今、一部ネット界隈で話題の台湾産パイナップルを食べました。
中国に急に輸入停止にさせられて台湾が非常に困ってたヤツですね。とにかく中国と言う国は何事も政治案件化してしまうので非常に困ったもんです(たぶん台湾に対するただの嫌がらせなんでしょう)。
この件を伝え聞いた日本では「台湾を助けよう!」運動がネットを中心に盛り上がっているようですが、それに便乗して買ってみました。
写真で判るように台湾産パイナップルは芯の所までまっ黄色で、芯ごと食べられるという噂は本当でした。
食べた感じですが、とにかく甘い、そしてジューシーです。芯の所を含めて果汁がたっぷりで、かじった瞬間果汁があふれ出して周りにこぼれまくる状態です。机の上に果汁をまき散らしてしまいました。
そして甘い。普通のパイナップルは酸味も結構あるんですが、このパイナップルに関しては葉っぱの付け根の部分は少し酸味を感じましたが(それでも通常品に比べると酸味が少なく甘みが強い)、中央部分はひたすら甘い。正直言ってかなりの驚きでした。
南国には結構行っていますが、ここまで甘いパイナップルは初めてでしたね。フィリピンの畑でとれた完熟パイナップルも非常においしかった記憶がありますが、それなりに酸味もあったので、味で言えばこの台湾産の方が上だと思います。
ただ気を付けなければならない所も2つあります。
1つは美味しいのでつい齧りついてしまうのですが、繊維は結構残っているので歯の間に挟まるという事ですね。特に皮に近い部分には繊維が結構残っているので、齧りつくのではなくメロンみたいにカットしてから食べた方が良いかもしれません。
また2つ目はジューシーすぎて果汁が飛びまくるのでテーブルの上もパイナップルを持っている手も果汁だらけになってしまうという事ですね。実際食べ終わった後で皮の部分を絞ったら、パイナップルジュースが取れました(少量ですが)。
まあこのパイナップルはおすすめですから、ぜひ食べてみてください。期待は裏切らないと思いますよ。ちなみに私はパイナップルを買ってきたのち4日くらい室温で追熟させました。
何事に対しても中国に対して謝意を感じることはありませんが、今回の件だけは中国に「輸入禁止にしてくれてありがとう」ですね。
成果報告会に行きました②
先日は午前中に参加した企業(設計部門改善)の成果発表会の状況を書かせてもらいましたが、今回は午後に参加した特殊部品製造メーカー(こう書かれると何の会社かわからない!)の成果発表会で感じたことを書かせていただきます。
このクライアントさんでは小集団型の改善活動を行っており、複数の工場で結構長い期間コンサルティングさせていただいています。今回参加させていただいたのは活動を始めて2年の工場で、基本的に選抜された複数チームに対して指導会を行っています(改善チーム総数はかなり多い!)。
今回の発表では多くのチームが「作業量に応じた工数管理」を主テーマとして取り組んでいましたが(担当コンサルが誘導した?)、成果的には非常に素晴らしい結果が出ており、平均で19.4%(前年対比)の生産性向上を実現しています。最も高い上昇率を示したチームでは35%(前年対比)の生産性向上を実現しており、1年でここまで変化させるためにはかなりの努力があったのではないかと思います(お疲れさまでした)。ちなみに生産性をここまで上げようとすると、個人レベルの頑張りや昭和的な気合と根性でどうにかなるものではなく、しっかりと部門管理の仕組みを作らないと実現できませんから(単なる作業改善では無理!)、製造管理面での仕組み改善をしっかりと行ったのだろうと思います。
他にも色々な発表がありましたし、中には工数管理には目もくれず、ひたすら品改善・不良削減に全エネルギーを振ったチームもありました(データ量がスゴイ)。今回の発表は全体として非常に密度の濃いもので、管理職のサポートも十分に受けた上での改善であり、非常に楽しく聞かせてもらいました(管理職にはもっとガンバレとコメントしましたが・・・)。
今回は小集団型の改善がベースになった活動でしたが、このタイプの改善を希望される企業さんは結構多いですし、実際に生産性向上につながるので私どもとしても良く提案させていただいています。ただ注意しないといけないのは「現場のボトムアップ型の活動」にしてはいけないという事です。なぜ? 小集団活動だからボトムアップ型(製造現場からの提案がベース)ではないの? と思うかもしれませんが、実はそこに大きなヒントが隠されているわけです。
今の小集団活動のベースは太平洋戦争後に荒廃した日本の製造業を立ち直らせるためにアメリカからデミング博士を呼んで始まったQC活動を発端としています。1970年代、1980年代には日本で相当流行りました(日本製品の品質向上に一役買ったのは間違いなく、デミング賞と呼ばれる賞もできた)。いわゆる品質問題を中心に活動していたのでQC活動と呼ばれていましたが、やがてテーマが生産性向上や作業改善などにも広がるようになり小集団活動と呼ばれることが多くなったような気がします。
日本では過去から欧米から来た改善手法や改革手法を大変有難がって崇拝する傾向があるのですが、年数がたつにつれやがて忘れ去られて「そういえばそんな手法あったね」と呼ばれるようになってしまいます(具体名を出すとヤバい感じがする)。ただその中でもしっかりと日本に根付き、全国にくまなく広がったのはこの小集団活動(QC活動)だけではないかなと思っています。
これには日科技連さんなどの努力の結果もあったと思いますが、私は小集団活動が日本人の気質に非常に合っていたのではないかと思います。グループメンバーで議論を繰り返し、みんなで考えて、みんなで行動する。そして努力の成果をみんなで分かち合うというスタイルが日本人の特性に合っていたんだと思います。多くの日本人はオタク体質ですから、疑問があれば徹底的に追及して原因を究明し、問題を解決してしまう所も小集団活動には相性が良かったんだと思いますね。
ただ当時は量産を前提とした「作れば売れる」時代であり、小集団の改善成果も生産量に比例して発現していましたが、残念ながら多品種少量生産環境が進展するにつれ改善成果はあまり出ないようになってきました。いわゆる低成長時代に入った1990年代からは小集団活動も低調になってきたように思います。やがて小集団活動は「そう言えば昔はよくやった」活動になったんじゃないかと思います。
ただこの小集団活動はやり方を変えれば今でも大きな成果を残せる活動であることは間違いありません。ポイントになるのが先に述べたボトムアップの所です。まあ簡潔に言うと「ボトムアップ」から「トップダウン」への転換が小集団活動で大きな成果を上げるポイントになります。つまり、活動テーマはトップダウン、具体的な改善行動はボトムアップというのが現代(多品種少量生産環境)における小集団活動のコツなんですね。
詳細は当社のホームページに書いてあるので参考にしてほしいと思いますが、当社ではそれを課題達成型小集団活動と呼んでいます(いろんなところでセミナーもやってます)。トップが広い視野で会社の中の問題(受注から出荷までの生産フロー上の問題)を小集団に提示し、それを小集団で解決していくというやり方ですね(目標管理に近いイメージもあるが、ちょっと違う)。ポイントになるのは管理職の動きと他部門との連携になります。分かり難いかもしれませんが、小集団とPJ活動、タスクフォース活動を混ぜて煮込んだみたいな感じです。
話が長くなってしまいましたが、小集団活動はやり方によっては今でも大きな成果が出せる手法ですし、日本人の特性にも合致しているやり方なので、今一度小集団活動に取り組んで見られたら如何でしょうか。思ったより成果が出るかもしれませんよ。
成果報告会に行きました。
昨日、午前と午後で2社の成果発表会に参加しました。午前中はWebで、午後からはリアル参加です(企業先で直接発表を聞くのは久しぶりです)。
午前に聞いたクライアント企業さん(一品受注型の製品を作っている)では設計改善を行って2年半が経っているのですが、標準化がかなり進んでおりそれに伴って設計効率も上昇しているようでした。チームによっては顧客との連携も取れ始めており、改善成果がしっかりと定着しはじめているようです。
またこのクライアント企業さんでは受注前の段階での情報収集、営業・設計間の連携に力を入れており(当社では受注前活動改善と呼んでいる)、上流段階で情報をしっかりとることによって下流工程(詳細設計)での混乱、手戻り、やり直しを防止し、設計効率が上がるような取組を行っています。当然ながら先に述べた標準化もこの動きに連動したものであり、標準化と事前情報入手で設計効率向上を実現しています。
同時にやっていることとして負荷管理と平準化がありますが、設計の場合は細かな日程管理を嫌う人もそれなりにいて進みにくい傾向があるのですが(まぁどこの会社の設計部門でもこのような傾向がある)、このクライアントさんでもそのような傾向は表れています。ただこのクライアントさんでは管理職が日程管理の目的と重要性をしっかりと理解しているので、遅いながらも確実に進んでいるようです。それに最近では設計の日程管理にも使えるようなITツールも色々と出ているので、比較的簡単に導入できたようです。
この日程管理というのは昔からあるし多くの人が知っていますが、これを確実に行えている企業は非常に少ないように感じます。まず日程管理をしっかりと行うためにはそれなりに精度の高いスケジュールを作れないことには始まりませんが、ここが出来ていない企業が多いんですね。それは精度の高いスケジュールを作るためには、設計上で行う各仕事がどれくらいの時間がかかるのかを知っていないとダメなわけです。製造でいうところの標準時間とは違い精度も範囲もかなりラフですが、この基準がないと案件ごとの設計時間や作業時間が見積れないわけです。
当然ながらこれらの時間がベースになって設計負荷を計算し、負荷調整や平準化を行っていくわけですから、この時間基準は非常に重要なわけです。そしてこの時間基準を作るためには日々の実績を記録することが必要ですし、各々のスケジュール(目標時間)に対して進捗を管理(記録)し、掛かった時間を精査してより精度の高いものを作り上げていく必要があるわけです。ですからスケジュール管理、日程管理といっても奥は相当深く、やり方によっては非常に大きな成果にもつながるし、ただやっているだけで何の効果も上がらないやり方もあるわけです。
実はここら辺が非常に説明が難しいんですね。私どもが企業さんに対してよくスケジュール管理は重要ですよという話をしますが、その背景にはこのような話があるわけです。ですから「その位当然やってますよ」と言われてもどの程度やっているかは細かく聞かないと分からないわけですし、その企業での管理状況を見て「もっと日程管理を強化しましょう」という話をしたときに「そんな当たり前のことをいまさら言われても・・・」という反応になったりするわけです。
知っている人も多いと思いますが、改善の第一歩は「見える化」なんですね。実際問題として問題点が見えるようにならない限り改善には着手できないわけです。今回お話ししたスケジュール管理も見える化の1つであり、どの程度まで「見える化」するかによって対策も変わってきますし、それによって得られる効果も違ってくるわけです。
今回のクライアント企業さんの日程管理(設計)は当社で指導するなかでは標準的なレベルですが、それでも大きな効果を生んでいます。大切なのは途中で止めずにしっかりとやりきることです。設計の改善手法も今回言及したスケジュール管理、標準化、平準化以外にもたくさんありますが、大切なのはしっかりとやり切ることですね。そうすれば必ず成果はついて来るもんです。
話が長くなったので、午後からの企業の話はまた後日書きたいたいと思いますので、よろしくお願いします。
トヨタが電気自動車を発表か!
自動車業界の人は既に知っていることだとは思いますが、いよいよトヨタが本格的にEV(電気自動車)に参入するようですね。
まあトヨタのことですからEVを作る技術は十分すぎるほど持っていたと思いますが、国内の自動車産業にとって超強烈なインパクトを与える内容ですから、発表時期を探っていたのかもしれませんね。
もしかしたら全個体電池(リチウムイオン電池などより高容量で短時間充電ができる電池。極めて性能が高い)の開発に目途がついたのかもしれません。現在のEVのネックは電池問題でしたから(ヒーターやエアコンを入れると航続距離が激減する)、ここに目途が付けばEVの利用範囲は急激に広がるので発表できると踏んだのかもしれませんね。
実際問題としてEVはモーター駆動になりますから、制御が非常に楽になるのは間違いありませんし、内燃機関エンジンと比べると部品点数が圧倒的に減ると言われています(一説によると3割くらい減るとのこと)。CO2の問題を抜きにしてもEVの方が今までの自動車よりも安くなることは間違いありませんし、操作性や安全性も格段に向上するでしょうから今後一気に広まることは間違いないと思います(要は電池の性能次第)。
またあのアップルが自動車を作るというのは確定路線みたいですし、日本の自動車メーカーに製造を委託するのではないかとも噂されています。たぶん発売されたら一定のシェアは間違いなく掴むでしょうから、その前に既成事実として「トヨタの電気自動車」のイメージを植え付けたいのかもしれません。
いずれにしても今後EVが主役になって行くのは間違いないでしょうが、そこで問題になるのは今までのエンジンメーカー、関連部品メーカーの挙動です。エンジン関連の部品は非常に多く、それらを作っているメーカーも数多くありますが、一挙に仕事量が減るのは明白なので今のうちから将来を見据えた動きを行う必要があるのですが、私の感覚で言うとその動きが非常に遅いように感じます。
EVはモーターで動かしますが、このモーターはエンジン部品(内燃機関部品)と違って細かなすり合わせ技術が必要ではないので、日本国内で製造する可能性は低いのではないかと思います。つまりEVの主要部品であるモーター類は世界最適調達のターゲットになり易く、コストの安い国で作ったものが大量に日本に入って来る可能性が高いという事です。もしかしたらEVの組み立て自体も海外で行い、日本には完成品輸入と言う形になるかもしれません。
政府はカーボンニュートラル(CO2削減)のために2030年にはガソリン車廃止!などと能天気なことを言っていますが(特にどこかの国のバカな環境大臣)、これによって日本の基幹産業である自動車業界が大ダメージを受けることになれば相当数の雇用が失われ、経済の低迷は間違いないのに何の手も打たずに放置していることは本当に信じられないですね。残念ながら今の日本で自動車産業からの人員を受け止めるだけの新たな産業はありません。
たぶんトヨタはその辺も十分に判っていたのでEVの発表を遅らせていたのでしょうが、とうとうタイムリミットが来たという事ではないかと思います。
EVの発展で自動運転や過疎地域での交通弱者の救済など便利な社会になるのはうれしいのですが、何となく素直に喜べないニュースでもありますね。
抗原検査を受けました
先日とある企業を訪問した時に新型コロナの抗原検査を受けました。よくTVなどで報道される抗体検査(新型コロナに対する抗体の有無を確認する)では無くて抗原検査(新型コロナウィルス自体を持っているかどうかを確認)です。まあ簡単に言うとPCR検査の簡易版みたいなもんですね。
基本的に外部から工場に立ち入る人には検査をお願いしているそうで、短時間(5分ほどで結果が出ました!)で結果が出るので使いやすいツールみたいです(精度はやや低いみたいです)。私の場合は(今回は)事務所の応接室で話をするだけで工場には入りませんから、先方は色々気を使って下さったのですが、私の方から「是非受けさせてください」と言って検査を受けました(実は大変興味があった!)。
結果は陰性で何の問題もなかったのですが、今回のコロナ禍はこういう所にも影を落としているのだなと思った次第です。
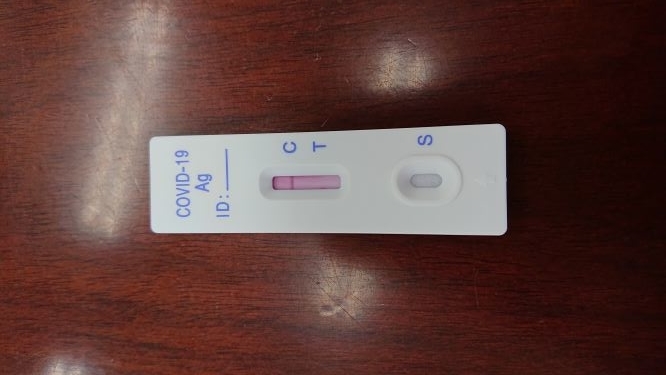
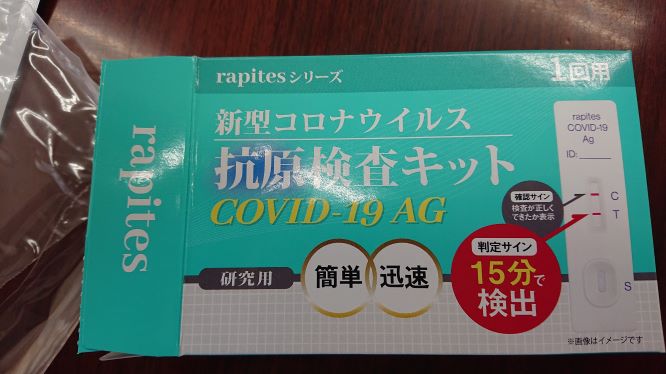
今回のコロナ禍は本当に産業の色々な部分に影響を与えています。私どものお客様でもコロナで大幅に受注が落ち込んだ企業もあれば、逆に仕事が増えた企業もありますが、ほぼすべての企業で新型コロナ対策に時間も費用も費やしており、大きな負担になっていることは間違いありません(企業としては対応をやらざるを得ない!)。
実際問題として新型コロナが流行り始めて1年がたち、コロナの性質も徐々に分かってきたように思いますが、本当にここまで厳密な対策が必要な病気なんでしょうか? 何となくTVや一部の感染症専門家(自称)が煽り立てているだけのように感じます。特に某都知事などは今回のコロナ禍を政治問題化し、国と対決している知事を演じようとしているだけに見えますね。
先日グローバルダイニング社が新型コロナ対策の妥当性をめぐって都を提訴しましたが(直接的には時短命令について)、この提訴に賛同する人も結構いるんじゃないかと思います。都に限らず政府もですが、飲食店をクラスター源と決めつけた対処を行っていますが、どうもその根拠は希薄なように感じます(それを示すデータが希薄)。私が思うに満員電車の方がよっぽど危険な気がしますけどね。まあいずれにしても何かしらのターゲット(批判の対象)を作っておかないと批判が都や政府に来ますから、飲食店がデコイ(おとり)にされただけのような気がします。
また、この件に関してはマスコミもどっち側で報道すべきか迷っているように見えますね(都側?企業側?)。一般的にマスコミは反権力を是としていますから企業側を応援したいんでしょうが、そうするとこれまでの報道姿勢(コロナは危険!)とは逆になりますから、どっち側で報道すべきか社内で議論をしている所だと思います。まあ意見がまとまらなかったら無視するという手もありますけどね(この可能性が高いと思う)。
いずれにしろ今回のコロナ禍で私が思ったのは、「マスコミ(特にTV)の影響力は捨てたもんでは無いなぁ」という事です。ネットの言論が強くなったと言われていますが、世間に対する影響力、拡散力はまだまたTVの方が強いように感じます。ネットの記事や動画に関してもTVや新聞がベースになっているものが多いですし、特に今回のコロナのような話題に関してはTVが最大の情報源になったように感じます(是非は別として)。
一方的な情報を大量に流し続けるというマスコミ戦略に対しては実はネットも同じような戦略を取っている部分もあります。アメリカ大統領選で明らかになりましたが、フェースブックやツイッターなど巨大な情報通信企業がトランプ氏が有利になりそうな情報は全てシャットアウト(検閲)し、情報の単一化を図ったのは記憶に新しいですね。
いずれにしろ、今回のコロナ禍で明らかになったのは強い情報伝達力を持った側が圧倒的に強いことですね。正誤に関係なく大量の情報を流せる側の論調が主導的になり、それを覆すのは中々難しいという事です。
結局、情報を制する者が世界を制するという事になるんじゃないかと、抗原検査の待ち時間中に色々考えてしまった私です。
勇気をもってコストを下げよう!?
先日「勇気をもってコストを下げよう」というタイトルでセミナーを行いました。大阪は緊急事態宣言が解除されましたので会場とWeb配信の2本立て、東京は緊急事態宣言が延長されたのでWeb配信のみで行いました。
たぶんタイトルを見て多くの人は??と思ったんじゃないでしょうか。コストを下げるのに勇気がいるとはどういうこと?、コストが下がるのはうれしい話なので勇気なんか関係ないのではないの?、といった感じではないでしょうか。
まぁ多くの人が?マークを付けるセミナーを行うことが実は結構あるのですが、セミナーを聞いて「なるほど!」と思ってもらえることが秘かな楽しみだったりするわけです。
先に種明かしをすると、一般的な製造業において「コストダウン=製造原価低減」な訳ですが、大幅に製造原価を下げようとする場合には工場全体の仕組みを変える必要があるので非常に難易度が高く、通常の改善レベルの取り組みではなかなか実現出来ないのでかなり気合を入れて取り組まないといけませんよということです。
具体的に言えば生産方式や工場運営の仕組みにバッサリとメスを入れることによってコスト構造を変化させ、低コスト体質に転換しない限り大幅な製造原価の低減はありませんよという内容です。
セミナーでは製造における仕組み改善と設計における仕組み改善の内容をお話ししましたが、この仕組みを変えるということが非常に難易度が高い改善なわけです。製造であれば生産方式(生産管理のやり方、モノの流れや情報の流れの管理方法)を変えて、短時間で一気に完成させる作り方、言わば工場内でモノが停滞せず、計画通りに、常に流れている理想的な状態を作り出しましょうという事です。そしてそれによってムダを削減し、労務費のみならず間接コストや管理コスト、品質コストも低減することによって製造原価を下げて行きましょうという事です。
当然ながらこのような改善は複数部門(製造・調達・生管・品管など)と協調しながら活動しないと実現できないわけで、明確な方針の下で強いリーダーシップをもって取り組まない限り実現できないため難易度が高いわけです。
また、「原価低減のために生産方式を変える」ということの必要性はある程度周囲に認識されたとしても、じゃあ実際にこの改善を行ったらいくらコストが下がるのか?と言われても明確に答えられないと言う問題もあります(全体最適型の改善は金額換算しにくい)。何となく良くなるのは分かるけど、具体的にいくら原価が下がるのかが分からない状態でこの改善PJに人を張り付けて、他部門の人の協力も得ながら活動を進めていくのにはかなり大きな困難があるわけです。いわゆる守旧派と呼ばれる人たちは、そこを突いてきますからね。
ですから「勇気」が必要なわけです。周囲から色々言われるかもしれないけど、大きな志を持って改善に取り組まなければ大きな成果は手に入れられないのです。そしてこのような取り組みを現実的に推進できるは誰かと言うと、もうわかると思いますがトップ(社長、もしくはそれに準じる人)しかいないわけです。
トップが旗を振って、複数部門の利害を調整しながら、ある時は強いトップダウンを出しながら進めて行かないと実現できないわけです。
今回のセミナーは、トップが強い覚悟を持って改善に取り組まなければ大幅なコスト構造の転換は実現できませんと言う内容であり、そしてその改善を上手に運営ていくためのヒントをお話しするセミナーでした。
セミナー後には多くの感想をいただいたので、そのうちまた同じ内容でセミナーを行うかもしれません。その時はまた多くの人に参加していただきたいと思っています。